A New Direction: Local Fiber and Design
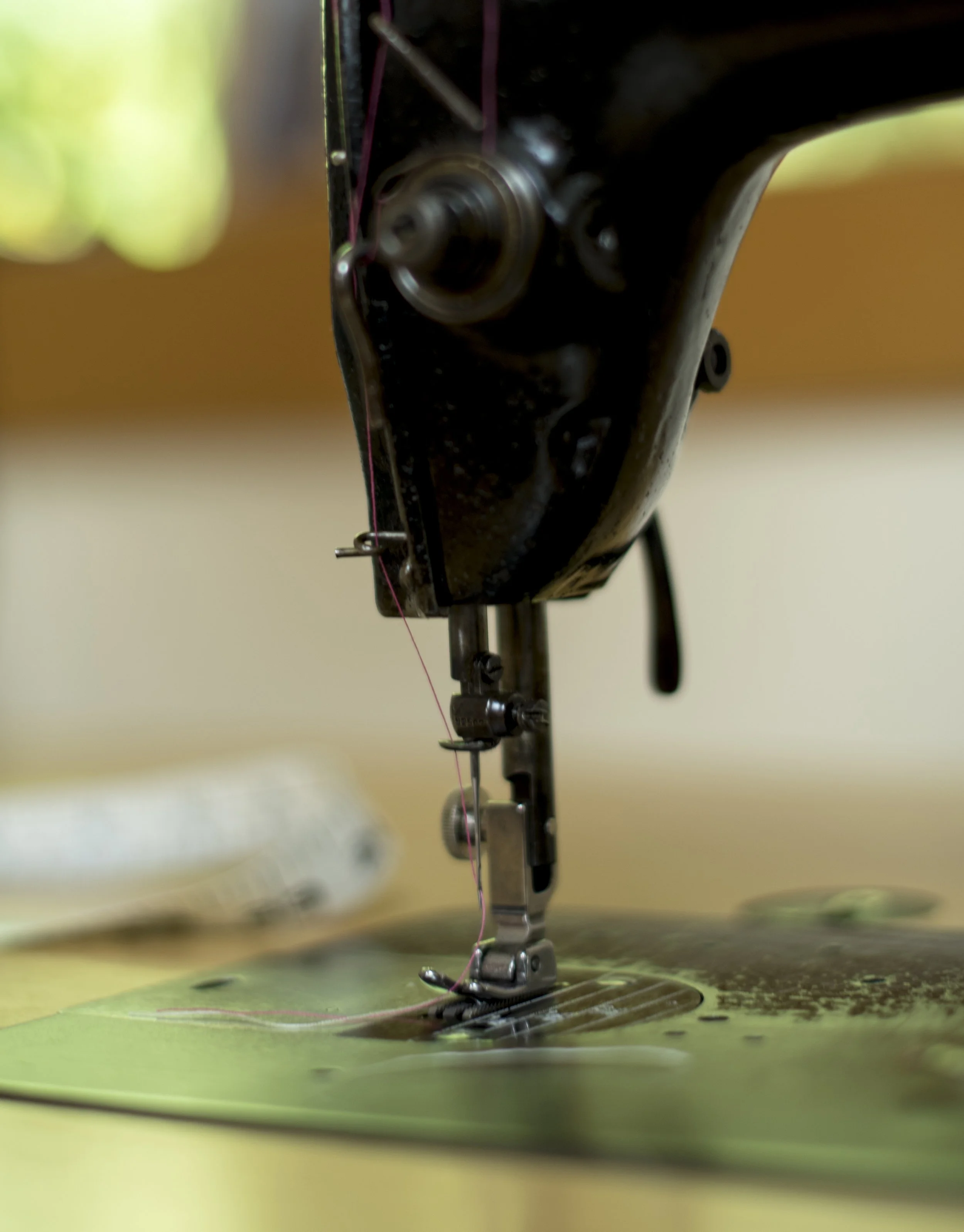
For the past five years, I have owned and worked in a fabric store on Bainbridge Island called Esther’s Fabrics. This island institution was opened by Esther Fox in 1959 and has been continuously operated on the island since. I loved running the fabric store. Having recently moved to the island from Virginia, it provided me an opportunity to meet people from across the island and from all over the world. I honed my sewing skills, and learned many new skills, along with learning more about business practices, bookkeeping, and taxes. As much as I loved the store, I decided I wanted to refocus my energy back to design and to free myself from the daily requirements of retail to a slower pace with a focus on design and an emphasis on fibershed, a philosophy of using locally grown and produced fiber, a philosophy modeled on the local food movement.
Pretty early in my career as an engineering professor, as I learned more about climate change and saw the waste in our systems, and having been raised by parents who had lived through the depression, I became dedicated to the idea of design for environment and design for reuse. In my time as an IBM manufacturing engineer, IBM offered what in the industry were known as FRUs or field replaceable units. They were various pieces of copiers that had a higher failure rate or a shorter life than other parts of the copier. Rather than scrapping the whole copier, only the faulty part could be replaced, leaving the larger unit in place, thus saving materials and replacement costs. What I saw in the late 1980s as we closed our domestic factories and sent manufacturing jobs overseas was the elimination of FRUs and the idea of planned obsolescence, the idea that you design for a product to have a limited life so that the customer would be forced to buy a new product as soon as part of that designed product failed. The marketplace started to change from companies that provided high quality customer service to focus more on product sales. Now three decades later we see a drop in product quality and a focus on selling more and more product and almost a complete disregard of the product’s impact on the environment.
To start, With Needle and Stick will be selling clothing that is produced from fabrics gleaned from local sources such as thrift stores and from scraps left from other sewing projects. As the quality of fabrics available in the resell market place decreases because of the prevalence of fast fashion clothing, I have turned my focus to regenerative agriculture, locally raised wool, and locally processed wool and natural dyes. Over the next year or so, I will be developing an approach to manufacture my own cloth from local wool and dyed with botanical dyes and use the resulting fabric to make clothing that can be reused and eventually composted.
I will be posting on my journey to this “new” model of clothing production, which is really just a return to the old ways of making our clothing before the industrial revolution, but using modern machines that are now available to us.